Quote:
Originally Posted by OLDKID
I know it's a popular mod , but in my opinion great if you were fabing up a arms from scratch with HEAVY wall chome moly . On stock thin wall mild steel a arms I can't see the benefit , surface area is reduced down to the diameter of the bung , and don't forget you're gonna be drilling through the back side of the tube for the threaded end to protude . My opinion : Reinforced tabs and good ball joints are better . More and broader surface area to distribute the work load . If riding hard enough to rip a tab off I think the arm will fail where drilled and bung welded in . Thin tubing ! 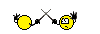
|
I got to differ with you on this one. Until you experience the difference you won't appreciate this conversion. A day and night difference. All the problematic issues associated with the yerf ball joint system are eliminated such as tracking, holding alignment, camber, along with adding strength and dependability. Ball joints are a traditional method and have proved dependable in countless applications but in this particular instance there is no such creature. I've built over a dozen sets for folks through the years with zero failures. My first set is over 10 years old going strong.
If the bungs are welded in correctly it becomes the strongest link in the system.
The first pic shows the bung in a piece of tube inserted into the end of the drilled A-arm. The second is the finished product. notice the inside of the A-arm is boxed.